Share
Pin
Tweet
Send
Share
Send

One of the masters proposed his own option for manufacturing fuel briquettes. If this occupation does not turn into a home or family business, then the result of these efforts you will certainly be able to melt your stove or solid fuel boiler.
The technology of manufacturing fuel briquettes step by step
Step One - Preparation
Even from some simple work in the carpentry workshop there are many sawdust. They can be prepared in separate bags to use in the future as the main raw material. The same applies to everything else that will be part of the briquettes, especially paper.
For drying and storage of briquettes, it is also worth highlighting a place closed from the rain. Over time, they can be stacked like woodpiles or bags.

The second step is the mold.
You can make the press yourself, for example, weld from corners and profile pipes. Precision is not needed here, the main thing is ease of use. The author was lucky to buy it ready.


The form for briquettes is set individually, based on the size of the furnace of your furnace. It is most reasonable to use metal, a sewer pipe made of cast iron, or steel, since pressing in even by hand will affect the integrity of its shape. Its main feature is the holes for the released moisture after pressing. The interval for them is arbitrary, but the diameter must be made so that compost does not come out through them during pressing (4-5 mm is enough).

The bottom of the mold is removable, and is not designed to be fixed during the pressing process.

It can be made from 30-50 mm thick boards or moisture-proof plywood. An interesting form was suggested by the author. Inside the cylinder, only 8-10 millimeters of plywood enters, while outside there is enough thickness to easily remove the bottom by hand. After the pressing is completed, the bottom is removed, and the finished briquette is squeezed out of the mold.


Another same detail must be done for the upper part of the mold, which will press on the compost.
Do not make the lever for the press short. Its length is directly proportional to the efforts you make to compress the material in the mold cylinder. The longer the lever, the less time and effort it will take to make briquettes.
The third step is to prepare the mixture.
Briquettes consist of two main components: 2 parts of sawdust and 1 part of paper. Sawdust, paper, cardboard, etc. are soaked in a separate container. They can not even be crushed, and it is best left for several days, completely covered with water. It is better to use hot water.

It is convenient to mix with a construction mixer with a drill, but you can also manually.

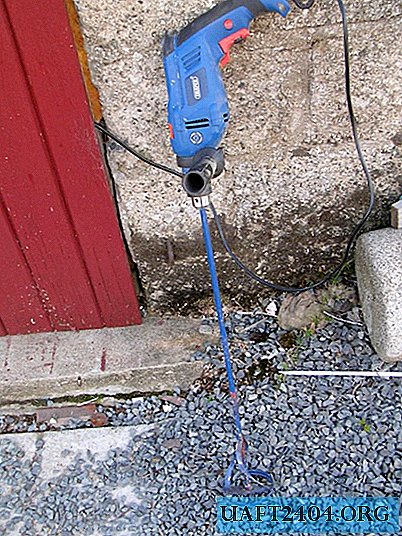
The finished compost is applied in small portions to the mold and is ready for pressing.


He claims that for small sawdust it will be necessary to increase its content, otherwise the briquettes will crumble.
Fourth step - pressing and drying briquettes.
Pressing can be done in several stages. With the mastered process, on average, it takes 30-40 seconds to make one briquette. The main task: squeeze as much moisture as possible from the compost.


After the batch of briquettes is ready, you can make a rack for drying under a canopy or outdoors in sunny weather.

Finished briquettes fit perfectly into bags, and are stored compactly, without taking up too much space. Such solid fuel has undoubted advantages. It does not cost money, does not require energy costs in the manufacture and allows you to get rid of garbage, waste for the benefit of the economy.

Use this technology for recycling materials, because it saves our natural resources!
Original article in English
Share
Pin
Tweet
Send
Share
Send